CFD performance vs. Wind Tunnel
- Paolo Casula
- Jun 12, 2024
- 2 min read
Updated: Apr 3

Unlike Wind Tunnel simulations, CFD enables not only testing the geometry at a 1:1 scale with the real Reynolds number, but also analysing millions of measurement points.
A wind-load benchmark simulation was conducted on a tall building, comparing 2 CFD solutions (VENTO AEC and ANSYS) to the Wind Tunnel test, using parameters from an academic study from the Eindhoven University of Technology¹.
Figure 1 shows the model of the 30-storey building with balconies, which was used in the Wind Tunnel test and replicated – with same scale – in the CFD simulations.
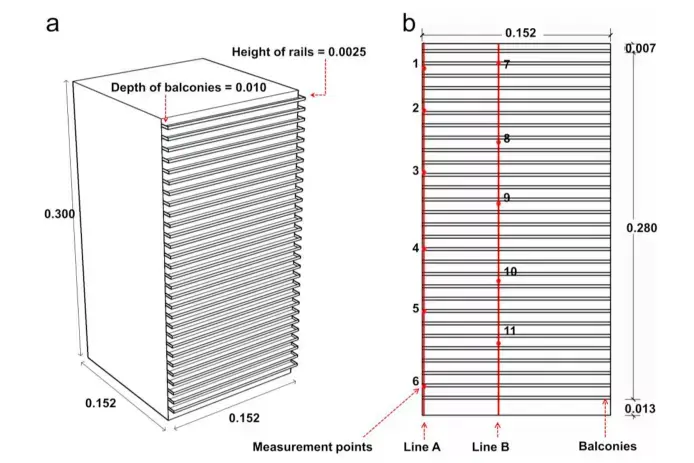
Figure 1: geometric model from the Wind Tunnel test.
The results of the benchmark are shown in Figure 2 , indicating the pressure coefficient related to Line B of the model.
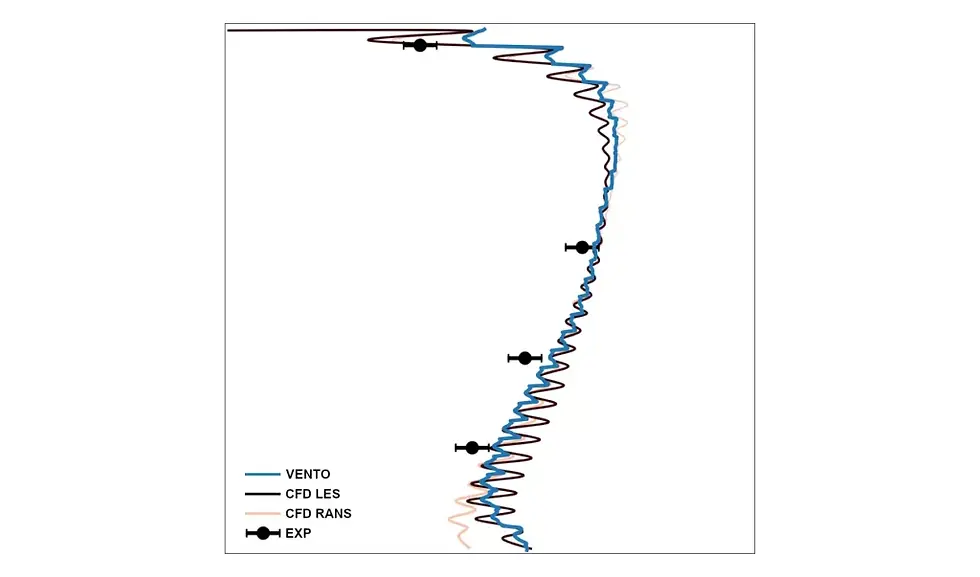
Figure 2: Pressure coefficient results from the benchmark between VENTO AEC, ANSYS and Wind Tunnel
The simulation with VENTO AEC was conducted with a mesh of similar complexity to the LES simulation in ANSYS, although using the RANS turbulence model.

Figure 3: modeling used in the reference paper and in the CFD simulations
Endorsed reliability
CFD has been used since 30 years in the aeronautical and automotive industries, proving it is a highly reliable alternative to wind tunnel tests.
FIA (Fédération Internationale de l’Automobile) and Formula 1 conducted extensive research and development using CFD, comparing the results with wind tunnel tests. These efforts revealed the accuracy of CFD and suggested that, while wind tunnel tests still provide real-world validation for the modeling in the virtual space, the majority of development work can be effectively conducted using CFD.
Notably, Formula 1’s chief technical officer, Pat Symonds, confirmed that 8 out of 10 teams expressed a desire to eliminate wind tunnels, solidifying CFD’s prominent role in the industry.
Read the full articles:
“F1 – FIRST LOOK: Formula 1’s 2021 car in the wind tunnel” on Federation Internationale de l’Automobile.“Eight out of 10 teams favor scrapping wind tunnels” on PlanetF1.
Great!