The Non-Conformal Grid technique from Vento: a disruptive innovation in CFD

Conformal grid
NON-Conformal grid
In Computational Fluid Dynamics (CFD), the mesh serves as a digital representation of the physical domain, dividing it into smaller elements for analysis.
Traditionally, CFD uses conformal meshes, in which all the nodes that define the object are also the nodes of the 3D mesh. However, this technique often leads to distortion of cells, particularly near objects, resulting in inaccurate calculations. Although sophisticated 3D mesh generators have been developed to address this issue, they are often time-consuming and technically challenging to implement.
The Non-Conformal Grid (NCG) technique developed by Vento is a game changer in the industry. With NCG, the mesh and the object’s nodes are treated as two separate entities: the shape and position of the object are reconstructed by proprietary NCG algorithms, independent of the mesh typology. The benefit? The ability to run accurate simulations, even on super complex geometries, without the need for simplification or “cleaning” of input files. This saves significant time and does not require highly technical skills.
What it means for you
Easy to use
With Vento, mesh construction is automatic. This means that CFD analysis can be done even by non-experts.
Faster turnaround time
Save up to 90% of pre-processing time, enabling quicker design iterations and increased productivity for you and your team
BIM ready
With Vento you can interact directly with the BIM environment and import extremely complex and realistic IFC models.
Making it tangible: case studies
Accurate simulation of complex architectural models: Meazza Stadium Milan
The Meazza Stadium is a complex architectural work, with a highly intricate 3D STL model (4 million triangles). With Vento, we were able to generate a three-dimensional grid around the stadium, accurately capturing the finest details of its structure, up to the single seats, stairs and fences. No cleaning of the model was necessary.
The entire setup, including grid generation of 100 mio cells, was completed in just 30 minutes. The subsequent runtime lasted approximately 15 hours (on cloud, 120 cores).
Vento’s GUI (Graphic User Interface) is extremely intuitive and allows to export a variety of outputs like Pressure Coefficient (CP) values and colour maps, tailored for the needs of the AEC professionals.
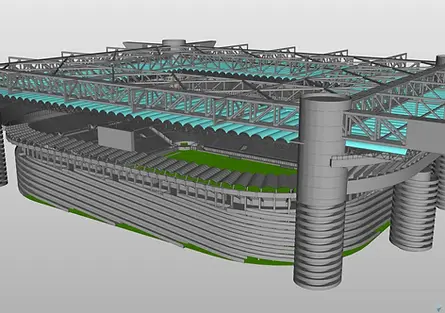
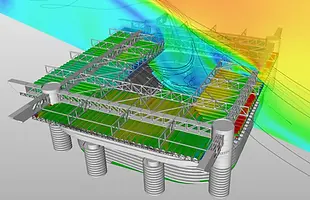
colour map
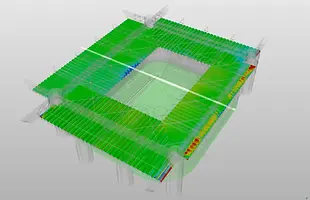
load on the roof

example of export results: CP values can be extracted on arbitrary sections

Massive reduction in pre-processing time: Telecommunication antenna
The objective of the simulation was to calculate the resulting forces on a telecommunication antenna (STL composed of 18.k triangles), by testing the performance of 3 different mesh levels: coarse (2.4 mio cells), medium (7.5 mio cells) and fine (32.9 mio cells).
The result demonstrates that the coarse, simpler mesh (2.4 mio cells) – which was generated in only 2 minutes – gave fully accurate assessment of the resulting force, differing from the fine mesh results by only 3%.
As a benchmark, the same simulation run with Snappy (the cut-cell mesh generator from OpenFOAM), led to a mesh as complex as 50 million cells without cleaning the STL.
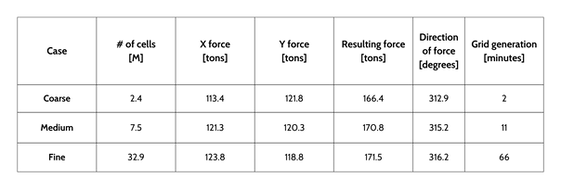
Wind Direction 315° – Wind Speed 28 m/s (100 km/h)
3D Conformal Mesh vs. Non-Conformal Grid Technique
3D Conformal Mesh
The 3D conformal mesh is a traditional technique used in computational fluid dynamics (CFD) simulations to create a computational grid around objects.
This approach involves creating a mesh in two steps: first, a two-dimensional mesh is created on the surfaces of the objects, and then this mesh is extended to fill the three-dimensional space with hexahedral or tetrahedral cells.
In the conformal mesh, the nodes defining the objects in the first phase are also nodes of the three-dimensional mesh, meaning that the mesh conforms perfectly to the surface of the objects. However, this conformity can lead to cell distortions, especially near objects, compromising result accuracy and requiring complex and time-consuming meshing.
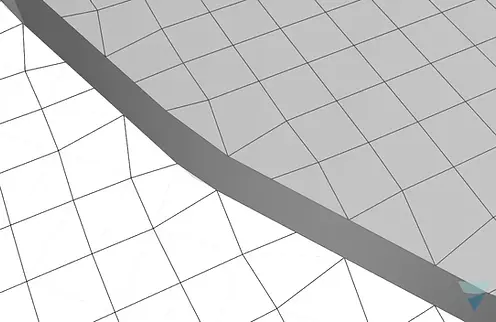
NCG Technique

The Non-Conformal Grid (NCG) technique created by Vento represents a disruptive innovation in the field of CFD simulations.
Unlike conformal meshing, NCG separates the mesh nodes from the objects, allowing for greater flexibility in grid generation and higher result accuracy. In NCG, the position of objects within the mesh is determined through the calculation of intersection points and normals to the objects’ surfaces
This avoids cell distortions near objects, enforces tangential velocity at the walls and maintains control over mesh size without the need to clean geometric models from details. This technique enables more accurate results and saves time and resources in the meshing phase, allowing for more efficient and precise simulation of fluid dynamic phenomena.